Market Snapshot: Medical disposables
Injection molded plastics couldn’t be more suited to the medical disposables
market. They bring not only cost efficiency and ease of processing in large
volumes, but also a host of performance benefits ranging from biocompatibility
and clarity to chemical resistance and sterilizability. For this and other
reasons, the outlook on IM plastics in this market remains sunny. According to
Fredonia Group (Cleveland, OH), the value of plastic resins consumed in
disposable medical supplies should rise 4.1% yearly, reaching $2.6 billion in
2011. If actual growth meets the prediction, it will mean consumption of about
1.4 billion pounds of resin.
Plastics retain a leading position among all raw materials in
disposable medical supplies, and the reasons, Fredonia says, include ongoing
innovations and improvements in polymer compounds. Such advances have made it
possible to meet performance criteria while upping quality and reducing cost. IM
plastic applications consist in part of hypodermic syringe cartridges, medical
kits and trays, and lab ware. Predictions from Fredonia are that improvements
and refinements in materials will increase the types of disposable medical
supplies created in commodity and engineered resins.
Market Dynamics
According to Ken Breeding, technology platform manager,
Eastman Specialty Plastics (Kingsport, TN), “Single use disposables, as opposed
to those that may be used and sterilized several times before disposal, are an
especially hot commodity right now.” The market currently favors ongoing
innovation focused on safety and cost, and both carry a lot of weight, Breeding
explains. “There is a trend toward disposables because they aid in cutting costs
and reduce the need to sterilize, but safety is the biggest reason for the
switch,” he says. “Needle protection is a key right now as a means of
controlling the spread of disease, which is an issue among healthcare
providers.” Micro fluidics, an emerging technology, is also a hot topic within
this market. It involves the precise control and manipulation of fluids that are
forced by geometry into sub-millimeter channels. OEMs are now developing micro
fluidic devices for drug discovery and diagnostics.
In the diagnostic world, instead of using a large quantity of
blood, lab techs could use a micro fluidic device with a drop of blood to test
for cholesterol, blood sugar, potassium, and more. These devices may also
produce results quicker, because there is no need to wait for a lab. “This will
shorten the time frame for analysis so that doctors can make quicker decisions,”
Breeding says. “Micro molding and laser engraving are two of the methods for
creating the micro channel; laser welding is typically used to seal the two
substrates.”
While this represents an opportunity for medical molders,
there are also challenges. Molders need to find a way to control internal costs.
Material prices are on the increase due to oil prices, so to protect margins;
molders need to find a way to improve efficiency internally via productivity
improvements and perhaps a focus on high volume products. Disposables are price
sensitive, so overhead reduction and automation are a big part of staying
competitive.
Future Opportunities
Disposables may not be limited to blood care products such as
stopcocks, luers, and syringes in the near future, according to Clare Frissora,
market director of healthcare for Sabic Innovative Plastics (Pittsfield, MA).
“There is a growing interest in disposable components for surgical instruments
as well,” she says.
Rather than dispose of the entire device, OEMs now are
investigating how to design instruments with dual components, one to be disposed
of and the other reusable portion to be cleaned and sterilized.
Frissora also notes a trend toward more concern about cleaner
and safer products. “What chemicals are being used, how are they being
sterilized, what is the total system cost to clean and/or sterilize? Even
disposable devices must be sterilized before use, and OEMs are looking at that
aspect.”
The current regulatory environment, both in the U.S. (FDA)
and globally, is influencing the selection of materials. “Our OEMs have to
respond to the tighter regulations and ask their suppliers for assistance,” she
adds. “For biocompatibility testing and assessment of materials, OEMs try to
pull from a range of materials that have already been assessed by the material
supplier.”
Cost containment is always an issue in healthcare, and
disposables are no exception. “If you consider the whole system, you find that
lower cost materials aren’t always the ones that produce the lowest part cost.
Customers are finding that they have to innovate, and are turning to suppliers
to find out how to do that at the lowest system cost.”
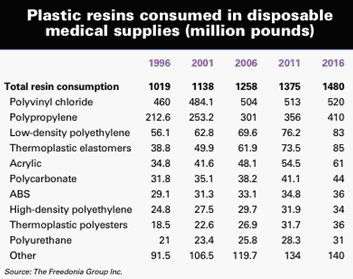
http://mpw.plasticstoday.com/imm/articles/market-snapshot-medical-disposables |