How Plasma Can
Aid Catheter Manufacturing
Leading Supplier Of
Instruments Systems And Technology, Henniker, Explains How Plasma Can Aid
Catheter Manufacture
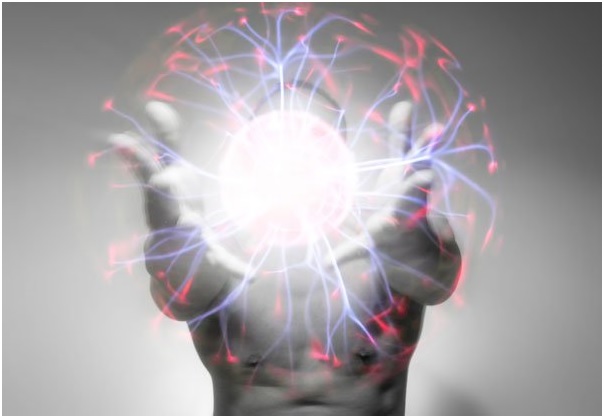
Catheter function and patient
health rely on strict material biocompatibility in order to prevent pathogen
introduction and propagation and to reduce instances of associated urological
and vascular problems.
Plasma surface modification is
proving to be a reliable and effective method for treating various component
materials, and also finished devices, in order to minimise the potentially
harmful side effects of catheter use.
Plasmas can be tailored to
deliver surface properties including anti-fouling, anti-microbial and increased
lubricity amongst others. They can achieve a range of desirable properties
either directly – by polymeric deposition – or indirectly, by introducing
intermediate functional layers prior to application of a final surface finish or
coating.
Plasmas are not a lab curiosity.
Plasma technology has been an important production tool for more than 30 years
in the fabrication of microelectronic devices for example. Over this period,
plasma technology has also permeated a much broader range of industries.
It’s useful to define what a
plasma is. Solid, liquid and gas are the three states of matter we are all
familiar with. We can move between the states by adding or removing energy (eg
heating/cooling). If we continue to add enough energy, gas molecules will become
ionised (lose one or more electrons) and so carry a net positive charge. If
enough molecules are ionised to effect the overall electrical characteristics of
the gas the result is called a plasma. Plasmas are therefore quite rightly,
often referred to as the fourth state of matter.
A plasma contains positive ions,
electrons, neutral gas atoms or molecules, UV light and also excited gas atoms
and molecules, which can carry a large amount of internal energy (plasmas glow
because light is emitted as these excited neutral particles relax to a lower
energy state). All of these components can interact with the surface during
plasma treatment. By choosing the gas mixture, power, pressure etc we can quite
precisely tune, or specify, the effects of the plasma treatment.
Many polymers used in catheter
manufacture are chemically inert and cannot bond easily to other materials,
displaying poor adhesion with inks, paint and glues. The reason for this is the
absence of polar and reactive functional groups in their structure. Plasma
surface activation renders many polymers receptive to other coatings. Oxygen is
usually used as the process gas, however, many plasma activations can also be
carried out with just ambient air.
Typical results for PU catheter
materials that were modified by plasma treatment and then heparin coated
revealed little or no protein binding after 30 days indwelling for example. In
another example, hydrogel adhesion and friction reduction improvement figures up
to 70% have been achieved by plasma treatment.
(Ref:
http://www.medicalplasticsnews.com/news/matter-inhand-how-plasm-can-aid-catheter-manufacturing/)
* * * * *
|