The Global
Medical Injection Molding Market
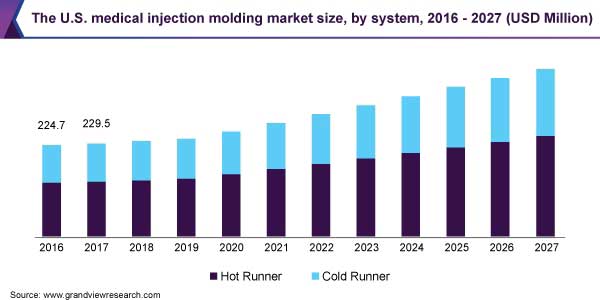
The global medical injection molding market size was
valued at USD 1.38 billion in 2019 and is expected to grow at a compound annual
growth rate (CAGR) of 8.2% from 2020 to 2027. The increasing demand for plastic
and metal injection molded components in the medical industry is expected to
drive the market over the forecast period. Moreover, the growth of the home
healthcare sector on account of the low costs involved as compared to hospital
care and intensive care has resulted in a rise in the demand for medical
devices. Different types of medical tests conducted by hospitals for diagnosis
have also contributed to the increasing demand for medical devices. The rising
geriatric population in the country, sophisticated healthcare infrastructure,
and relatively higher disposable income levels are some of the key factors
driving the healthcare industry in the U.S. In addition, the country has the
highest healthcare spending in the world.
Factors, such as ISO certifications & compliance,
FDA regulations, material properties, suitability in extreme conditions, and
durability are taken into consideration during the manufacturing process.
Materials such as silicone, polycarbonate, polyethylene, and polypropylene, are
widely used in the medical injection molding process. It is one of the primary
processes that many companies adopt to manufacture medical products by using
plastic as well as metal materials.
System Insights
The hot runner system held the largest market share
of over 55% in 2019 and is expected to exhibit the fastest CAGR over the
forecast period. Hot sprinter molds consist of two plates, which are heated
using a complex framework. This framework maintains the temperature of liquid
thermoplastics at the same level as their warming chamber. As a result, the
demand for the hot runner system is high.
Moreover, several benefits of hot runner system
including faster cycle time and lower pressure requirement to push the molten
mixture into the mold cavity, as well as the elimination of waste due to the
absence of runners, accommodation of larger parts with a higher volume of
production, and improvement in consistency & quality of parts, are augmenting
the segment growth.
The use of cold runner system depends on its
advantages, such as easy maintenance and cost-effectiveness; it is suitable for
various types of polymers. This system is a feasible option as it can produce
higher quality parts. Therefore, the application of cold runner systems is
growing at a significant rate owing to lower initial investments compared with
other systems.
In addition, flexibility in designing options,
capabilities of handling a variety of engineered thermoplastics, and flexibility
in gate locations, which can be easily changed or upgraded, will boost the
demand for cold runner systems. However, the demand for hot runner is higher
owing to its better efficiency.
Class Insights
Class III medical device segment accounted for 38.4%
of the overall revenue share in 2019. Class III medical devices, such as
defibrillators, ventilators, respirators, and oxygen therapy equipment, are
anticipated to have a significant demand on account of the COVID-19 pandemic.
The growing adoption of injection molding to manufacture medical device
components is projected to drive the segment growth over the forecast period.
Overall 10.0% of all the medical devices fall under
this category. These devices are capable of handling the substantial risk of
injury and are designed with the balance of strong cyber security control and
easy accessibility. Class III includes devices such as implanted pacemakers,
heart valves, and cerebral simulator.
Injection molding is used to produce a broad range
of medical components; it widely used processes in mass production. It has the
ability to produce components and small disposable goods with high precision.
Growing adoption of injection molding to produce numerous parts and components
of Class I medical devices is expected to have a positive impact on market
growth over the coming years.
The Class II segment is projected to register the
fastest CAGR over the forecast period. Injection molding offers several
advantages over other methods, such as lower risk, higher safety, and high
productivity. Furthermore, the growing penetration of plastic injection molded
products in the medical industry is expected to drive market growth over the
forecast period.
Material Insights
The plastic material segment in the medical industry
accounted for 76.0% of the overall revenue share in 2019. Engineering grade
plastic resins are beneficial when used for the manufacturing of medical and
pharmaceutical products as they have high tensile strength, metal tolerance, and
temperature resistance. Furthermore, they also reduce waste, weight, and the
overall cost of production.
Plastic injection molding is a feasible technique
for manufacturing complicated designs of medical products. Demand for
medical-grade injection-molded products is increasing as they are durable,
naturally resistant to contaminants & chemicals, and offer economies of scale to
large scale firms. As a result, the penetration of the material is expected to
witness significant growth.
(Ref.:
https://www.grandviewresearch.com/industryanalysis/medical-injection-molding-market
).
|