
Invited Speakers Profile & Abstracts :
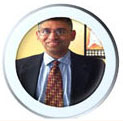 |
Dr. Ajay
Padsalgikar
Senior Principal Scientist
DSM Biomedical in Exton
Pennsylvania, USA |
Profile Summary:
Dr. Ajay Padsalgikar, USA, a Well-Known Personality in this versatile field
has agreed to be the Keynote Speaker. He is working as a Senior Principal
Scientist at the Innovation Center of DSM Biomedical in Exton, Pennsylvania,
USA. He has more than 30 published scientific papers and 10 patents. In
2017, he wrote a book titled “Plastics in Medical devices for Cardiovascular
Applications” that was published by Elsevier.
Title :
Global Trends in Medical Plastics Technology and Applications – Role
of Indian Industry
Abstract
Health care is expanding worldwide with the
industry showing double digit growths in emerging economies. The use of
polymers within this sector is increasing with the growth of the industry as
well as with new approaches in medical treatment. This talk will focus on
the suitability of plastics for medical applications, the manufacturing
processes for medical device production, emerging applications and
opportunities for the Indian industry.
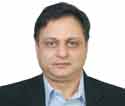 |
Mr.
Ajay Pitre
Managing Partner
Pitre Business Ventures LLP |
Profile Summary :
A
pioneer in India since 1973, the Sushrut-Adler Group has specialized in the
manufacturingand distribution of cost effective orthopaedic solutions
adhering to international standards.
Mr Pitre’s width of experience was as a Managing Director of the Sushrut-Adler
group for more than 25 years. Mr. Pitre took charge of the group operations
as ‘Managing Director’ in 1987 after he graduated in commerce. He further
completed a course in ‘Management for Small and Medium Enterprises’ at The
Indian Institute of Management. While handling the diversified activities of
Sushrut – Adler Group such as indigenous development of relevant technology,
manufacturing, marketing, sales and finance. He also led associations with
various foreign companies for technology transfer and implementation of
manufacturing under know-how transfer. Mr. Pitre has set for himself high
standards of performance to excel in the areas of strategic planning,
implementation and resource management. The group had achieved noticeable
milestones under Mr.Pitre’s exceptional leadership qualities and vision over
the last two decades.
He has been the past Co-Chair & is currently the Advisor of the Medical
Device Forum of FICCI (Federation of Indian Chambers of Commerce and
Industry).
Mr. Pitre is a member of Governing Board CMTI (Central Manufacturing
Technology Institute).
He is a member of the board of a (Medical) Technology Business Incubator
being established at the Shree Chitra Tirunal Institute for Medical Sciences
and Technology (Department of Science & Technology) being seed funded by
Department of Science & Technology, Government of India.
He is also a member of various committees of professional organizations such
as FICCI Healthcare Committee, CII Healthcare Committee, and Sub-Committee
for standardization of Orthopaedic Implants of the Bureau of Indian
Standards (BIS), Governing Council-Maharashtra Chamber of Commerce, Industry
& Agriculture (MACCIA).
Mr. Pitre is a member and the past Chairman of CII (Confederation of Indian
Industries) Medical Technology Division. He has been a part of the
Committees interacting with the Indian Regulators on evolving current
Medical Device Regulations and Implementation Strategies. Mr. Pitre has also
been a Co Opted Member of Committee of Administration of Pharmexcil.
Mr. Pitre is on the Board of Trustees of Pitre Foundation and CREDAR. Pitre
Foundation is a funding trust through which Pitre Family executes its
various social initiatives. The Foundation works in close collaboration with
CREDAR (Centre for Rural Entrepreneurship) which is the executing trust with
area of operation in Devrukh (Dist. Ratnagiri).
CREDAR executes social, cultural and educational projects through various
local NGOs, namely 'SIDDHI', 'AAKAR' (dedicated to Rural Community
Development, raising Environment Awareness, Women and Youth Welfare), DCAD
(Dedicated to Educational Activities), LKAD (Cultural activities) etc.
CREDAR was established with a view to offer training facilities and avenues
to enable the youth to undertake employment for Self Sustenance.
In 2003, The Indian Orthopaedic Association honored him with a ‘Certificate
of Excellence’ in recognition for the contributions to the Orthopaedic
fraternity in India.
In Sept 2010, he was invited as a guest speaker in New York by Wells Fargo
Securities to present his thoughts and ideas on broader Indian Medical
Device market and the Indian orthopedic industry.
Being an Industry spokesman, he has been invited as a speaker at prestigious
forums to cover general aspects of the orthopaedic industry as well as the
Medical Device Industry namely the ‘Orthotec Europe conference’ in Zurich on
“Emerging market opportunities, challenges and key drivers”, The ‘Australian
Medtec conference’ in Melbourne. These forums also include premium Medical
and Engineering institutes, Conferences by CII, FICCI, Stanford India
Biodesign and government bodies such as Department of Biotechnology, Office
of the Scientific Advisor Govt. of India, Board of Health Ministry of India,
and Department of Pharmaceuticals.
Mr. Pitre was invited for a Panel discussion by World Bank to discuss
‘Opportunities and Challenges for the Medical Device Industry in India’ at
The World Bank, New Delhi.
Mr. Pitre has also moderated various discussions including one at the Asian
Harmonization Working Party (AHWP) workshop at New Delhi.
Mr. Pitre’s has long been convinced about the relevance of Indian Innovation
in medical technology and business models to help meet the growing need of
the emerging non-affluent world that constitutes more than 80% of the global
population. After enabling the Sushrut-Adler Group to take larger steps by
becoming part of Smith & Nephew, a global orthopaedic leader, Mr. Pitre
supported the acquired organization as it’s Chief Mentor. Now as Managing
Partner of Pitre Business Ventures LLP. he continues his connect with the
Medical technology Industry by engaging in various activities including
assisting, consulting and enabling various MedTech companies and innovators
in aiming to catapult the Indian MedTech industry to become a powerhouse
while catering to almost 80% of the global population with cost and market
appropriate solutions relative to the affluent countries.
Mr. Pitre is also a certified Marshall Goldsmith “Executive Coach”.
Mr. Pitre is a resident of Pune (Maharashtra, India). As a student he was a
keen sportsman and a passionate Cricketer too.
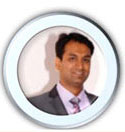 |
Dr. Suneel Bandi, PhD
Technology Leader Medical
High Performance Polymers, Americas |
Profile Summary
:
Sunil Bandi Holds a
Doctoral Degree in Macromolecular Science and Engineering from Case Western
Reserve University, with a broad polymer industrial experience.
Presently Global Technology
Leader - Medical (implant and non-implant) for EVONIK's High performance
polymers group.
Prior to joining Evonik,
Lead product development at Solvay and has Management consulting experience
in the domain of technology based market and strategy assessment at
Newrycorp.
Lead startup Aeroclay Inc.
a novel platform technology for lightweight applications.
Dr. Suneel Bandi is well
connected to global network of medical customers, and
actively support technical programming.
Title: High Performance Polymers for Medical Device Applications
Abstract:
EVONIK is a technology
leader for high-performance polyamides, EVONIK’s current portfolio of
specialty polyamides include PA12, PEBA (flexible polyamide), bio-based
polyamides, and transparent polyamides for the medical devices. From
catheters and balloons to diagnostic equipment and surgical instrumentation,
VESTAMID® Care and TROGAMID® Care are well established. EVONIK offers
flexibility in the design and manufacturing through our new Bonding VESTAMID®
Care and TROGAMID® Care grade polymers. EVONIK’s VESTAKEEP® Care PEEK
materials are used in temporary contact and instrument applications, while
VESTAKEEP® PEEK i-Grades are used for permanent implant applications. From
spine and sports medicine, to drug delivery devices and heart valve
applications, new compounds of VESTAKEEP® PEEK are designed to meet the
specific application needs and performance demands of medical-device
industry.
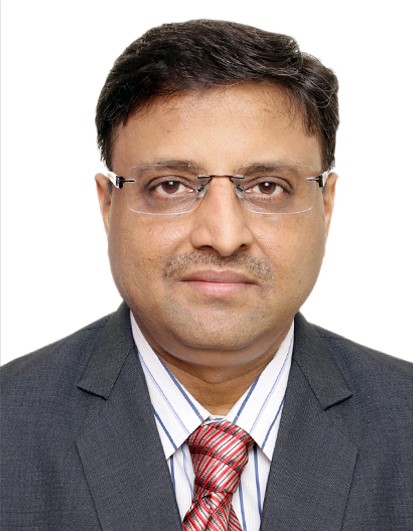 |
Mr. Umang Shah
National Sales & Marketing Manager - Masterbatch & Compounds for Medical
& Pharma Segment
CLARIANT Chemicals India Ltd, Mumbai |
Profile Summary
:
CLARIANT is one of the world’s leading
Specialty Chemicals company. Mr. Umang Shah is a National Sales & Marketing
Manager for Masterbatch & Compounds for Medical & Pharma Segment (HPS) since
Dec, 2015 and based at head quarter in Navi Mumbai. He is helping Indian
manufacturers to develop various Medical devices & Pharma packaging
applications meeting the regulatory requirements for the domestic & export
markets.
Mr. Umang Shah is a Polymer Technologist, MBA
– Marketing with over 25 years of experience in reputed MNCs. Earlier, he
worked with SABIC Innovative Plastics & GE Plastics for more than 22 years.
He has rich Techno- Commercial experience and handled various key
responsibilities as a
-
Key Accounts
Manager – Sales & Marketing.
-
Application
Development Specialist.
-
Technical
Services Manager at Mumbai.
He has worked on various segments like
Automotive, Electrical, Appliances, Medical and Industrial projects.
Successfully developed several Metal to Plastics, Themoset / Glass to
Thermo-plastics applications.
Also, worked at Engineering Plastics
compounding plant at GE Plastics (now SABIC), Vadodara, Application
Development Centre at Gurgaon, GE’s Global R&D Centre at Bangalore on
various innovative and Patent projects.
Mr. Umang Shah is Immediate past Chairman of
Indian Plastics Institute (IPI) – Mumbai Chapter. With this, He is helping
Plastics industry and students to organize, seminars, conferences for the
latest updates.
Title : Polymer Compounds &
Masterbatch from CLARIANT - Helping You Deliver Safe Treatments Globally
Abstract
-
Clariant at a glance.
-
Healthcare Products & Process for new developments.
-
What
is Important/ Interesting for Customers ?
-
PROTECTION of healthcare products:- end to end solutions from API to
patient.
-
Focus on Regulatory changes: USP 661.1, ICH Q3D
-
Why
CLARIANT ?
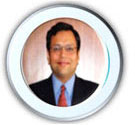 |
Mr. Aditya Kumar
Managing Director
Marco Polo |
Introduction :
Company founded
in 1999 and began with offering 3D printing services to the industry using
FDM technology. Gradually started services using SLA AND SLS techniques and
also offering a range of parts using Vacuum Casting and RIM. Over the last 5
years the company has been actively engaged in manufacturing tools and
supporting supplies for Injection Moulding.
Personal :
Polymer
Engineering from Pune University and masters in Plastics Engineering from
USA. Have been associated with 3D printing technology technologies for last
20 years primarily in the field of automotive applications and development
of medical devices.
Topic : Use of additive manufacturing
technologies for development of medical devices
Abstract :
1. Brief history of
3D printing
2. Applications for prototyping
3. Various industry verticals using 3D printing
4. Use of 3D printing for medical applications
5. Specific applications in detail including
- Pre surgery models
- Dental applications
- Hearing aids
- Other medical devices
6. Future expectations from the technology
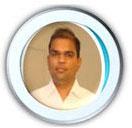 |
Dr.
Amol Chaudhari
Director, Research and Development
SynThera Biomedical Pvt. Ltd. |
Profile Summary :
Education : pH.D.
in Biomedical Science
Professional Career :
1. SynThera Biomedical Pvt. Ltd., Pune, India
- Director, Research and Development
2. Savitribai Phule Pune University, Pune, India - Postdoctoral Fellow
3. University of California, Davis, USA - Postdoctoral Fellow
Honors / Awards :
1. Dr. D. S. Kothari Postdoctoral Fellowship
(Postdoctoral Position at Savitribai Phule Pune University)
2. Katholieke Universiteit Research Fund (PhD Research at Katholeieke
Universiteit Leuven)
Publications :
1. Research Papers, Reports: 20
2. Others: 1 PhD Thesis, 6 Conference Presentations
Title : Glass Foam As Bone Graft Matl.
Abstract :
There is a
clinical demand for artificial bone graft materials which has interconnected
pores and resorbable structure that stimulate bone regeneration. Bone graft
materials of bio-active glasses are very efficient in bone regeneration due
to the virtue of bone-stimulating resorption. If porosity can be included in
such glasses, then their functionality can be further enhanced due to their
possible use as integrated scaffold. One of the commonly used glass
manufacturing processes is in-situ polymerization with added glass powder
wherein gas-forming (or foaming) agents are used to form bubbles in the
solid mass which resembles foam. Glass particles are incorporated in the
bulk of such foam. Thus formed foam is then heated to a temperature at which
the glass particles fuse together and the foam structure is retained made
only of glass. There are many parameters that are required for obtaining
suitable foam. In the presentations following points will be discussed:
• Specific
applications of glass foam in biomedical field
• Controlling the bioactivity of such glass foams
• Different foaming agents and their effect on the bioactivity of foam
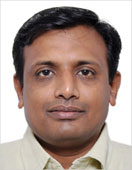 |
Dr. Sachin Jain
Founder Director
SKYi Composites Pvt.
Ltd. |
Profile Summary
:
Dr. Sachin Jain is a founder Director of SKYi
Composites Pvt Ltd and SKYI Innovation LLP.
Sachin studied Polymer Engineering from University of Pune, India, and
Masters from University of Akron, OH, USA. He worked on a sponsored project
at NASA on nano-composites and bio-degradable polymers. Subsequently, he
worked at Dainippon Ink and chemicals Inc. Japan on nano-structured blends
of UV-curable polymers for flexible displays and artificial heart
transplants. He then continued his studies at Eindhoven University of
Technology, Eindhoven The Netherlands. His PhD thesis challenged long
perceived theory of Einstein on filled polymers. His research was cited as
”HOT paper“ in 2005 in Scientific journal “SOFT MATTER” and awarded with the
Golden Thesis Award for his PhD thesis.
He started his professional career at BASF-SE,
Ludwigshafen, Germany as a Research Scientist, and later became Director of
Research and technology at DSM. In 2015, he founded SKYi as a part of a
larger objective of being a global leader providing sustainable solutions in
the field of polymer technology. Sachin has accrued more than 27
international patents and has published more than 14 papers; some of his
papers have been cited as “HOT” papers by scientific journals. He has also
been invited to deliver over 40 high-level academic lectures and
presentations around the world. He can be reached at sachin.jain@skyi.com
Title :
Bio-absorbable
composites for supporting medical implants
Abstract :
The paper presents
biodegradable composites which be process as conventional glass fiber
reinforced polymers, where polymer matrix is chosen from commercially
available environmental friendly bioplastics such as PLA, PBS etc. The
reinforcing glass fiber degrades in controlled environment.
Bio-absorbable composites
using long fiber reinforcement technology gives high strength and stiffness
to material which can replace conventionally used metal supports specially
used for orthopedic surgeries. Earlier attempts to use absorbable composites
lacked the strength and life for such applications and importantly also the
cost. Advances in the medical grade glass fibers combined with SKYi’s
proprietary long fiber composites manufacturing technology is expected to
provide successful alternative. The challenge remains on availability and
cost of medical grade glass fibers.
Most importantly, these
bio-degradable composites can be processed on conventional injection molding
machines.
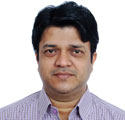 |
Mr. Lokesh Upadhye
Leister India |
Title :
Advanced Laser Welding For Medical Devices
ABSTRACT
Plastics are part of our everyday life. It has
transcended in to all aspects of our life including necessities in addition
to desires. From diapers to clothing to gadgets to cars to medical devices,
plastics is everywhere. As the parts are getting complex, the need to join
the moulded components is getting more demanding. The weld must be strong,
hermetic with a process that is consistent, repetitive, CLEAN and ECONOMICAL
TO RUN.
Laser technology is the cleanest method to assemble plastic parts. There is
no particle dust formation. Moreover, it leaves minimal or zero stress
behind making it the most suited technique for medical devices. Laser being
a focused source of energy can melt plastic in quick time. As it is one of
the latest technical advancements, it is expensive than the more established
techniques. However, concentrated energy of laser means that we can use
fraction of energy of other techniques to melt plastics. Again, laser can be
used in different source formats to get the most out of available energy.
Leister, a renowned name worldwide in plastic
welding and process heat, is a Swiss origin company that has added Laser and
Infra-red technologies to meet customer demands. Leister provides 6
configurations of laser source to suit the part to be joined making it
possible to provide an economical, energy efficient, assured technique to
weld plastic medical devices. With a pan India footprint of 10 sales,
service offices, Leister is committed to be with customers from pre-sales
consultancy to post-sales support.
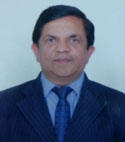 |
Mr. Rajesh
Gera
Asst. Vice President - Business Development
Reliance Industries Ltd., PET Division, Mumbai |
Profile Summary
:
Mr RK Gera is
working as AVP-Business Development in RIL-PET Division. He joined Reliance
in Dec’ 97 and has handled Technical Services, Sales & Marketing, Product
Development and is now responsible for the “Business Development, Recycling
and Sustainability initiatives”.
His focus is on ‘Application Development, Market Promotion & Sustainability’
for PET. He is primarily involved in development of Indian markets for
‘Pharma, Edible Oil, Milk & Dairy Products, Paint..& establishing new PET
resins He supported Major Pharma companies to launch their products for
first time in PET in India. He has worked closely with Beverage majors like
Amul & RoohAfza in successfully launching their products in RELPET bottles
in India.
He is a B-Tech in Plastics Technology from HBTI, 1985 batch. He earlier
worked in LG Polymers (Product Development and Technical Services of
Polystyrene and EPS) & in FGP (Technical Services & Market Development of
FRP and Glass Fibre Tissue products). He was involved in developing and
promoting FRP Underground Petroleum Storage Tanks for first time in India
with the Oil majors among other FRP/FRTP applications.
He had been the key initiator of 2 International conferences on ‘Packaging
of Edible Oils in PET’ in India in ’06 and ’07 in Mumbai and Agra resp.
These seminars were well attended by major EO manufacturers from all-across
the country & it changed the way; Edible oils are today packaged in PET in
India
In today’s seminar, he will share views on ‘PET Plastics Applications in
Pharma Industry’. He will cover ‘PET bottles for Pharma products, Blood
Collection Tubes (BCT) and thermoformed APET sheet products & blisters. As
he has been actively working on ‘Recycling & Sustainability’ initiatives for
PET, thus in conclusion he will update us very briefly on the Reliance’s
participation in Sustainability Initiatives in India. Over to you Mr Gera..
Title : PET Plastics Applications in Pharma
Industry
ABSTRACT
PET Bottles are
being have been used in India for more than 2 decades now in India. These
are used for many of OTC products including antacids, cough syrups,
vitamins, ..etc. PET has replaced other conventional materials used in
Pharma sector and it has proved to be a more greener packaging option for
pharma products. The PET packaging for Pharma products include ‘Bottles,
Blood Collection Tubes (BCT) and thermoformed APET sheet products &
blisters’. PET bottles are one of the most recycled products in India as
recycled bottles. These are primarily used for making fibres/fabrics and
hence contribute towards a more sustainable and greener world. |